Function of solenoid valve in pneumatic system
31.03.2024
In the complicated world of pneumatic systems, knowledge of solenoid valve operation is essential. These solenoid valve function in pneumatic system centers, directing the flow of compressed air to perform precise mechanical tasks. It is impossible to overstate their significance to the automobile and manufacturing sectors. We investigate the basic operation of solenoid valves in pneumatic systems. Can see how crucial they are to advancing automation, dependability, and efficiency by looking into their types, purposes, and functions.
Working principle of On/Off solenoid valve
The electromagnetic principle drives the operation of the On/Off solenoid valve. A magnetic field is produced by the solenoid coil when an electric current is introduced to it. This magnetic field forces the plunger, or armature, to move inside the valve body. Regarding the On/Off solenoid valve, this action opens or closes the valve to permit or forbid the flow of gas or liquid.
There are two primary states for a valve: open and closed. When the is in normally open pneumatic valve, the armature or plug rises, allowing gas or liquid to pass through it. The armature, or plunger, is lowered in the closed condition, on the other hand, to obstruct the passage and halt the flow.
Components of an On/Off Solenoid Valve
Understanding the essential components of an On/Off solenoid valve is essential to understanding how the device works.
- Solenoid Coil: Understanding the essential components of an On/Off solenoid valve is essential to understanding how the device works.
- Plunger or Armature: The armature, often known as the plunger, is a moving component located inside the valve body. It moves in reaction to variations in the magnetic field after being magnetically drawn to the solenoid coil.
- Valve Body: The plunger, armature, and fluid or gas channel are all located within the valve body. When it is closed, proper alignment and sealing are guaranteed.
- Spring: In certain systems, a spring helps return the plunger or armature to its initial position when the electric current is cut off by acting as a mechanical force against the magnetic pull.
Application of the solenoid valve
Due to their adaptability, durability, and ease of use, solenoid valves are extensively utilized in a wide range of sectors. Solenoids are essential to a wide range of systems and processes due to their ability to regulate the flow of gases and liquids as well as the motion of mechanical parts. The main uses for solenoid valves are listed below, along with a few drawbacks and benefits for each.
1. Industrial Automation
Solenoid valves are crucial to industrial automation because they regulate the flow of various fluids, including water, oil, and air, in both pneumatic and hydraulic systems. They are necessary for tasks like controlling the movement of actuators, cylinders, and robotic arms, which raises the efficiency of production and assembly lines.
2. Water and Irrigation Systems
In drip irrigation, sprinkler, and pipeline systems, solenoid valves control the flow of water. In agricultural and landscaping applications, resources are used and preserved thanks to the exact control these valves offer over water distribution.
3. HVAC (Heating, Ventilation, and Air Conditioning) Systems
Refrigerant and steam flows are managed by solenoid valves, which are essential components of HVAC systems. They are necessary, for instance, to regulate the coolant flow in air conditioners, the water flow in heating systems, and the airflow in ventilation systems.
4. Medical Equipment
Diagnostic tools, anesthetic machines, and ventilators are a few medical devices and technologies that heavily depend on solenoid valves.
They guarantee precision dosing and delivery by offering exact control over the flow of gasses, liquids, and pharmaceuticals in crucial healthcare situations.
5. Automotive Industry
Numerous automobile applications, including fuel injection, pollution control, and transmission systems, require solenoid valves.
They enhance fuel economy, smoother engine operation, and overall car performance and dependability.
Advantages of Solenoid Valves
1. Fast Response Time: The fast opening and closing times of the pneumatic solenoid valves allow for quick control of fluid flow and system operation.
2. Remote Operation: Pneumatic solenoid valve function automated processes and remote monitoring by interfacing with electronic control systems.
3. Compact Design: Because solenoid valves are made of lightweight materials and have a generally compact design, they are perfect for applications where weight or space are limited. Their small size makes installation flexible in areas with limited space.
4. Energy conservation: Solenoid valves use extremely little electricity when operating, which reduces overall operating costs and encourages energy conservation. For a variety of applications, they are inexpensive and environmentally friendly choices because of this advantage.
5. Various Configurations: There are many different types of solenoid valves, such as 2-way, 3-way, and 4-way valves. This adaptability allows for tailored solutions to meet the specific requirements of different applications, which improves flexibility and adaptability.
Disadvantages of Solenoid Valves
1. Restricted Pressure and Temperature Range: Certain solenoid valves may not be suitable for use in specific high-pressure or high-temperature applications due to limits on the maximum pressure and temperature they can tolerate.
2. Vulnerability to Electrical Failure: Solenoid valves can malfunction due to power outages, electrical surges, or faulty components because they are dependent on energy to function.
3. Possibility of Leakage: Poor installation or gradual deterioration may lead to solenoid valve leaks, which can reduce the efficacy and efficiency of a system.
4. Maintenance Requirements: Solenoid valves require routine cleaning, lubrication, and inspection to ensure proper performance and prevent issues like clogging or corrosion.
5. Cost: Solenoid valves can be more expensive than other valve types, despite having a number of advantages over other valve types, particularly in high-performance or specialized applications.
Difference between direct acting and piloted solenoid valves
The two main types of solenoid valves that are frequently used in a variety of industrial applications are piloted and direct-acting. While controlling the flow of gases or liquids is the common goal of both types, there are differences in their designs, functions, and applicability for various applications. In the sections that follow, the differences between piloted and direct-acting solenoid valves will be covered, along with a few situations in which one might be better than the other.
1. Direct-Acting Solenoid Valves
The three primary components of a direct-acting solenoid valve are the solenoid coil, plunger, and valve seat. The solenoid opens the valve to the flow of gas or liquid by producing a magnetic field that forces the plunger higher. Unlike piloted valves, direct-acting valves just depend on the magnetic force produced by the solenoid coil; they don't need external pressure to operate.
Advantages
- Simplicity: The streamlined design of direct-acting solenoid valves, which has fewer components, makes maintenance and repair processes easier.
- Fast Response Time: These valves provide accurate control over flow rates and system operation by opening and closing quickly.
2. Piloted Solenoid Valves
The auxiliary pilot valve on piloted solenoid valves controls the flow of gas or fluid to the main valve. The solenoid adjusts the pressure differential across the main valve to activate the pilot valve, so achieving precise control over the flow.
Unlike direct-acting valves, piloted valves function by the combination of direct and indirect forces. By regulating the flow of gas or liquid through the pilot valve, the solenoid opens or closes the main valve.
Advantages
- High Pressure Capability: Direct-acting valves are not as good at managing high pressures as piloted solenoid valves are. They are therefore perfect for applications needing reliable performance in demanding settings.
- Variable Flow Control: Piloted valves provide more flexibility in controlling pressure and flow rates. The incorporation of a pilot valve facilitates accurate modification, hence permitting optimized regulation in complex pneumatic systems.
When to Use Each Type
- Direct-Acting Solenoid Valves
Use direct-acting solenoid valves where low pressure operation, fast response times, and user-friendliness are essential. Applications requiring precise control at lower pressures include water dispensing devices, small-scale automation projects, and low-pressure pneumatic systems.
- Piloted Solenoid Valves
Use piloted solenoid valves for applications that need high-pressure control, variable flow rates, and precision regulation. For instance, when pressure differentials are significant, precise flow management is necessary to maintain operational efficiency and safety in pneumatic actuators, hydraulic systems, and industrial processes.
Types of solenoid valves
Solenoid valve in pneumatic system because they provide accurate control over the flow of gases and fluids. Selecting the ideal solenoid valve for a particular pneumatic system requires understanding the many types of solenoid valves. Solenoid valves come in a variety of kinds, each designed for a specific use and environment.
Description of Different Types of Solenoid Valves
Two-Way Solenoid Valves
Two ports make up Two-Way Solenoid Valves (2/2 Valves): an intake and an outlet. Through the opening and closing of the channel between these two ports, these valves control the movement of gas or fluid.
Popular Models
- Norgren Solenoid Valves (2/2 Series 82160): These valves are recognized for their compact design and high flow capacity.
- Burkert Solenoid Valves (Type 6013): Featuring a durable brass body, these valves offer a wide range of voltage options.
Three-Way Solenoid Valves
Three-Way Solenoid Valves (3/2 Valves) consist of three ports: an exhaust, an outlet, and an intake. These valves allow you to control and redirect the flow of gas or liquid between two separate paths.
Popular Models
- SMC Pilot Operated Solenoid Valves (SY5000 series): These valves are renowned for their compact design and high flow rates.
- Burkert Solenoid Valves (Type 6014): Featuring a stainless steel body, these valves offer excellent corrosion resistance and long-lasting performance.
Four-Way Solenoid Valves
Four-Way Solenoid Valves, sometimes referred to as 4/2 or 4/3 valves, have two input ports, one outlet port, and one exhaust port placed in different combinations. Complex control over the flow of gas or fluid, including reversing and stopping, is made possible by these valves.
Popular Models
- Norgren Solenoid Valves (4/2 Series 83460): Renowned for their versatility and compatibility with different media types.
- Burkert Solenoid Valves (Type 6014): Features a compact design and high switching frequencies.
Pneumatic solenoid valve
A pneumatic solenoid valve is a type of solenoid valve used in pneumatic systems to control the flow of gases in pneumatic systems, such as compressed air, using electromagnetic principles. These valves are made up of a solenoid coil, an armature or plunger, and a valve body with intake, output, and exhaust apertures. When electricity is given to the solenoid coil, it moves the armature or plunger, opening or closing the valve. Thus, a magnetic field is produced. This feature regulates the flow of gas or compressed air used in industrial, commercial, and automotive contexts. It enables precise control of actuators, cylinders, and other pneumatic components.
Description of a Pneumatic Solenoid Valve
- Solenoid Coil: The solenoid coil is typically made of copper wire wound around a cylindrical form. When energized, it generates a magnetic field that attracts the plunger or armature.
- Plunger or Armature: The plunger or armature is a movable component within the valve body. It is magnetically attracted to the solenoid coil and moves in response to changes in the magnetic field, thereby opening or closing the valve.
- Valve Body: The valve body houses the plunger or armature and contains the ports for inlet, outlet, and exhaust. It ensures proper alignment and sealing when the valve is in the closed position, preventing leakage of compressed air or gas.
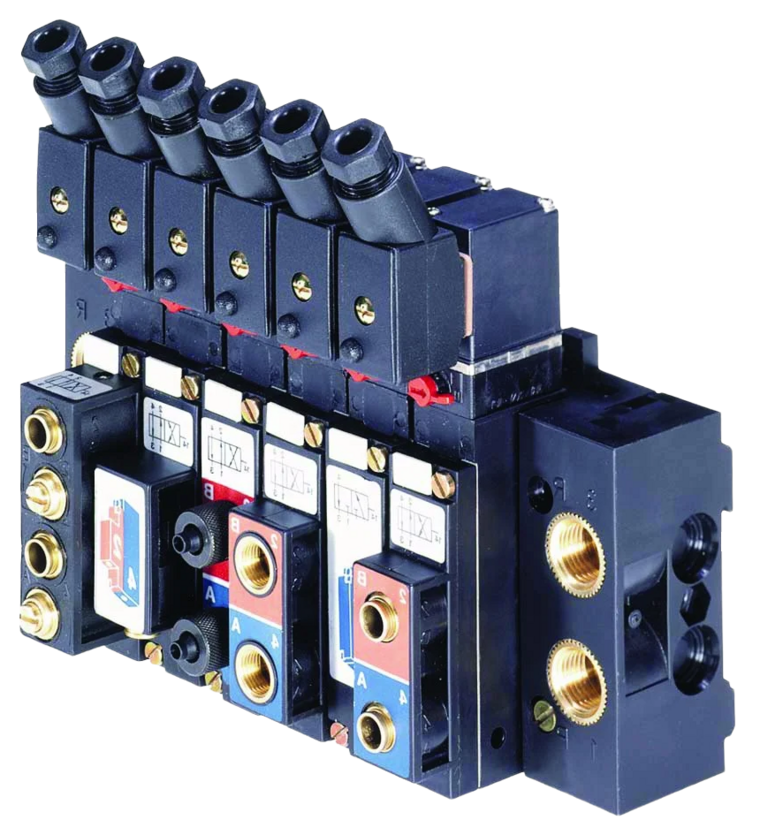
Advantages of Pneumatic Solenoid Valves
Quick response times from pneumatic solenoid valves provide for precise and timely control of pneumatic systems.
- Dependability: These valves have a reputation for being strong and dependable, which qualifies them for demanding industrial and automotive applications.
- Compact Design: Because pneumatic solenoid valves are usually lightweight and compact, it is simple to install and incorporate them into small pneumatic systems.
- Energy Efficiency: Solenoid valves add to the inherent energy efficiency of pneumatic systems by using very little electricity when in use.
- Versatility: A broad range of pneumatic applications across several industries are served by pneumatic solenoid valves, which come in a variety of sizes and designs.
Conclusion
Pneumatic systems rely heavily on solenoid valves because they offer accurate control over the flow of pressurized air or gases. Their influence is felt in a number of industries, as they facilitate the operation of pneumatic equipment.
Pneumatic system integration of solenoid valves necessitates meticulous planning, taking safety protocols, reaction time, and sequencing into consideration. Designing and implementing reliable and effective systems is made easier when suppliers and pneumatic experts work together.
Consider factors such as pressure rating, flow rate, voltage requirements, and environmental conditions when selecting a solenoid valve for a specific application to ensure compatibility and optimal performance. Appropriate installation and maintenance are essential to keeping these valves reliable and long-lasting while preventing issues like leaks, corrosion, and malfunctions.
Solenoid valves are essential to the operation of pneumatic systems because of their precise control, durability, and efficiency. Through comprehension of their operations, appropriate valve selection, and adherence to installation and maintenance protocols, it is possible to improve system efficiency, productivity, safety, and economy.