Omron Rotary Encoder
19.07.2024
Precision tools called Omron rotary encoders translate an axle's or shaft's angular position or motion into an analog or digital output. These encoders are essential for providing accurate feedback in various motion control applications. Essentially, they act as sensors that track rotational position and speed, translating mechanical movement into readable electronic data.
Importance in Industrial Automation
Rotary encoders are vital components in industrial automation systems due to their ability to provide precise and reliable position feedback. Here’s why they are so important:
1. Precision and Accuracy
In industrial automation, precision is paramount. Omron rotary encoder ensure that machinery operates with high accuracy, essential for tasks such as cutting, assembly, and inspection. Accurate position feedback helps maintain the quality and consistency of products, reducing waste and improving overall efficiency.
2. Enhanced Control
Rotary encoders enable precise control over motion systems. By providing real-time feedback, they allow control systems to adjust motor speeds and positions dynamically. This level of control is crucial for complex automation tasks, such as robotic arm movements or conveyor belt operations, where timing and synchronization are key.
3. Reliability and Durability
Industrial environments can be harsh, with exposure to dust, moisture, and extreme temperatures. Omron rotary encoders are designed to withstand these conditions, ensuring reliable performance over long periods. Their robust construction minimizes downtime and maintenance costs, making them a dependable choice for industrial applications.
4. Versatility in Applications
Omron rotary encoders are ideal for a broad range of applications in a variety of sectors due to their adaptability. They are used in manufacturing to control machinery and monitor production lines, in robotics for precise movements and positioning, and in the automotive industry for tasks like steering control and throttle position sensing.
5. Integration with Modern Technologies
As industrial automation evolves, integrating advanced technologies like IoT and Industry 4.0 becomes increasingly important. Omron rotary encoders are compatible with these technologies, allowing for enhanced data collection, remote monitoring, and predictive maintenance. Industries benefit from this integration by having more efficient operations, lower operating costs, and optimized processes.
6. Safety and Compliance
Accurate position feedback from rotary encoders contributes to the safety of automated systems. By ensuring that machinery operates within specified parameters, encoders help prevent accidents and ensure compliance with safety regulations. This is particularly important in industries such as automotive and aerospace, where safety is paramount.
Types of Omron rotary encoders
Electronic devices called Omron rotary encoder translate rotational or angular movement into an electrical signal. The rotational speed, angular displacement, or absolute shaft position can then be determined using these signals.
Omron rotary encoders come in two primary varieties: omron incremental encoder and omron absolute encoder. Every variety has benefits and drawbacks, therefore it's critical to select the best kind for your specific use.
Incremental encoders
Omron incremental encoder measure angular displacement by counting the number of pulses generated as the shaft rotates. These pulses are generated by a slotted optical disk or a magnetic disk with poles crossing the sensor.
Advantages:
- Simple design
- Inexpensive price
- High accuracy
- Wide speed range
- Resistance to noise
Disadvantages:
- They do not maintain the absolute position of the shaft
- A reference signal must be used to determine the initial position
General characteristics:
- Resolution: from 1 to 65536 pulses per revolution
- Rotation speed: up to 30,000 rpm
- Shaft diameter: from 3 to 35 mm
- Output type: NPN, PNP, RS422
- Supply voltage: 5 V, 12 V, 24 V
Absolute encoders
Omron absolute encoders are used to find a shaft's absolute position, or its location with relation to a fixed point. A code disc with a different code for every shaft position is used to do this. The sensor reads the code and transforms it into a digital signal that shows the shaft's exact location.
Advantages:
- They maintain the absolute position of the shaft
- Do not need a reference signal
- Quick and accurate positioning
Disadvantages:
- A more complex design
- More expensive price
- Limited speed range
General characteristics:
- Resolution: from 1 to 65536 positions
- Rotation speed: up to 6000 rpm
- Shaft diameter: from 3 to 35 mm
- Output type: NPN, PNP, RS422
- Supply voltage: 5 V, 12 V, 24 V
Key Features of Omron Rotary Encoders
Omron rotary encoders are renowned for their superior performance and reliability, making them a staple in industrial automation. Here are the key features:
- High Precision: encoder omron offer exceptional accuracy, essential for tasks requiring precise motion control, such as CNC machining and robotics.
- Durability: Designed to withstand harsh industrial environments, these encoders are resistant to dust, moisture, vibrations, and extreme temperatures, ensuring long-lasting performance.
- Versatile Output Options: They provide both incremental and absolute outputs, catering to a wide range of applications and ensuring precise feedback for different needs.
- Compact Design: encoder omron come in space-saving designs, making them easy to integrate into various systems, even those with limited space.
- Reliable Signal Transmission: Advanced signal processing minimizes noise and interference, ensuring clean and consistent data output.
- Energy Efficiency: These encoders operate with low power consumption, contributing to reduced energy costs and enhanced sustainability.
- Customizable Options: Omron offers customization to meet specific application requirements, such as varying shaft sizes, mounting configurations, and output types.
- Enhanced Safety Features: Equipped with diagnostics and fail-safe mechanisms, these encoders provide early warnings and help prevent operational failures.
- Easy Integration: They facilitate smooth integration with current industrial systems by supporting a variety of interface options and communication protocols.
How to choose the right Omron rotary encoder
Choosing the right Omron rotary encoder is an important step in ensuring your system performs optimally.
There are many factors to consider when choosing an encoder, so it's important to have a clear understanding of your needs and requirements. Here are some key points to consider:
1. Understanding your program
- What is the function of the encoder? Do you need an encoder to measure rotational speed, angular displacement or absolute shaft position?
- What is the speed range of your shaft?
- What resolution do you need? (Number of pulses per revolution)
- What type of output signal do you need? (NPN, PNP, RS422)
- What supply voltage do you need? (5 V, 12 V, 24 V)
- What dimensions and weight should the encoder be?
- Does your program have any mounting restrictions?
2. Consideration of environmental conditions
- Under what conditions will the encoder be used? (Temperature, humidity, vibration, dust, chemicals)
- Do you need an encoder with IP protection?
- Is shock and vibration resistance important?
3. Evaluation of technical characteristics
- Compare the characteristics of different models of Omron encoders.
- Pay attention to features such as resolution, accuracy, rotational speed, output signal type, supply voltage, dimensions, weight, and environmental resistance.
It is also important to consult with a specialist from Eltra Trade - an Omron distributor, to help you choose the right encoder for your specific application.
Remember that choosing the right encoder can make a big difference to the performance and reliability of your system.
Troubleshooting common problems with Omron rotary encoders
Omron rotary encoders are reliable devices, but like all electronics, they can sometimes fail. Here are some of the most common problems you may encounter and how to fix them:
1. Signal errors
- No signal: Make sure the encoder is correctly connected to the controller. Check the cables for damage or kinks. Check the encoder supply voltage.
- Noisy signal: Make sure the encoder is installed in a clean and dry place, away from sources of vibration and electromagnetic radiation. Check the grounding of the encoder.
- Incorrect signal: Check encoder resolution and controller settings. Make sure the encoder output signal type is compatible with the controller.
2. Mechanical malfunctions
- Hard rotation: Check the shaft for dirt or dust. Check that the shaft rotates freely. Check the encoder bearings for damage.
- Shaft stop: Check if the shaft is overloaded. Check whether there are no mechanical obstacles on the shaft. Check for damaged couplings or connections.
3. Problems with electricity
- Short circuit: Check the insulation of the cables. Check the encoder housing for damage. Check for a short to ground.
- Overvoltage: Make sure that the encoder supply voltage corresponds to the rated voltage. Use a protection diode to prevent reverse current.
- Power loss: Check the power supply. Check fuses and circuit breakers. Check the power cables for damage.
Other problems
- Incorrect programming: Check the controller settings. Make sure the controller software is compatible with the encoder.
- Incorrect installation: Check the encoder installation instructions. Make sure the encoder is set correctly.
Successful implementation of Omron rotary encoders in various industries
Owing to their dependability, precision, and adaptability, Omron rotary encoders are extensively utilized throughout diverse industries. Here are a few instances of Omron encoders being successfully implemented:
Automotive industry
- Electric power steering: Omron encoders are used to measure the angular position of the steering wheel, which allows precise control of the electric power steering and ensures smooth and comfortable steering.
- ABS system: Omron encoders are used to measure the rotation speed of each wheel, which allows the ABS system to prevent the wheels from locking during braking and to ensure stability and control on slippery roads.
- Traction Control System: Omron encoders are used to measure the rotational speed of each wheel, allowing the traction control system to distribute torque to the wheels to prevent skidding and provide better traction.
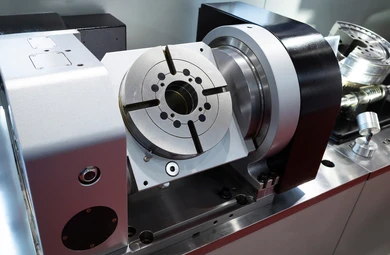
Machine building industry
- CNC machines: Omron encoders are used to precisely position the machine axes, allowing the machine to process parts with high precision and quality.
- Robotics: Omron encoders are used to measure the angular position of the robot's joints, allowing the robot to perform complex movements with high precision.
- Conveyor systems: Omron encoders are used to synchronize the movement of conveyors, which allows products to be transported smoothly and efficiently.
Packaging industry
- Filling machines: Omron encoders are used to precisely dispense products into bags or other containers.
- Labeling machines: Omron encoders are used to accurately place labels on products.
- Conveyor control: Omron encoders are used to synchronize the movement of conveyors, allowing products to be transported smoothly and efficiently.
Medical equipment
- MRI scanners: Omron encoders are used to precisely position the patient in the scanner, allowing for high-quality images.
- X-ray machines: Omron encoders are used to precisely position the X-ray tube and detector, allowing for clear and precise images.
- Surgical robots: Omron encoders are used to measure the angular position of the robot's joints, allowing the surgeon to perform complex operations with high precision.
These are just a few examples of successful implementation of Omron rotary encoders. Omron encoders are used in a wide range of other industries, and their use is constantly increasing due to their many advantages.
Conclusion
Omron rotary encoders are an essential choice for any production environment that values precision, reliability, and efficiency. These devices ensure accurate position and speed feedback, which is critical for optimizing the performance of automated systems. With their robust construction, Omron encoders withstand harsh industrial conditions, offering long-term durability and reducing maintenance needs. Their high precision and versatile output options cater to diverse applications, from CNC machining to robotics.
The compact design of Omron encoders allows for easy integration into various systems, even in space-constrained environments. Advanced signal processing ensures reliable data transmission, while energy-efficient operation helps lower overall energy costs. Customizable features enable tailored solutions to meet specific requirements, enhancing the flexibility and effectiveness of your automation processes.
Choosing Omron rotary encoders means investing in high-quality, dependable technology that enhances the productivity and reliability of your production systems. Their superior performance and adaptability make them a top choice in the field of industrial automation.
Eltra Trade offers a large catalog of Omron encoders, featuring fast worldwide delivery and the best prices. Rely on us for prompt service and competitive pricing to meet all your industrial automation needs.