Ultrasonic Level sensor working principle
10.05.2024
In today's world of industrial automation, for several procedures, precise and trustworthy liquid or bulk material level measurement is essential. Sensors for ultrasonic levels are available to the rescue by offering a non-contact and accurate measurement method that is widely used in various industries. This article gives an overview of the the advantages and functionality of ultrasonic level sensors, applications and future prospects.
Ultrasonic Level Sensor Principles Explained
The quantity of solids, liquids, or slurries within a specific container or area can be using ultrasonic level sensors to measure, which are multipurpose instruments used in industrial automation. What makes these sensors unique is their non-contact measurement technique, measuring the separation between the sensor and the surface of the material utilizing a high-frequency sound waves. These sensors are versatile and widely used in industries such as water treatment, chemical processing, food and beverage production, and pharmaceuticals. To understand how these sensors work, let's explore their key components and the principle of operation.
Key Components of Ultrasonic Level Sensors
Included in an level sensor is several key components that work together to measure distance accurately. These components include:
- Transducer: The transducer is the heart of the ultrasonic level sensor. It transforms electrical power into ultrasonic sound waves and vice versa. When measuring level, it emits high-frequency sound waves that travel through the air or other media.
- Receiver: The receiver is typically part of the transducer unit. It detects the reflected ultrasonic waves after they bounce off the surface of the material being measured.
- Signal Processor: The signal processor interprets the data received from the transducer. It calculates the time taken for theuse ultrasonic waves to reach the surface and return, allowing it to determine the distance and, consequently, the level of the material.
- Display or Output Interface: This component displays the measured level or provides an output signal to a control system. It allows operators to monitor the level and make defensible choices depending on the data.
Working Principle Explained
Ultrasonic level sensors are crucial in automation technology for measuring the level of various substances, from liquids to solids. Their principle of operation is rooted in the use of ultrasonic waves to calculate the distance between the sensor and the surface of a material. This non-contact measurement technique is valuable in environments where physical contact could be hazardous, disruptive, or cause contamination. Let's dive into the understanding the ultrasonic level sensor's operating principle how they operate.
Here's how it works
1. Emission of an ultrasonic pulse:
- The transducer generates a short ultrasonic pulse that has a high frequency (typically 20kHz to 200kHz).
- This pulse is focused and directed downward into the tank by means of a transducer.
- The emitter can be piezoelectric or electromagnetic.
- The pulse energy passes through the liquid or bulk material.
2. Reflection of the pulse:
- When the pulse reaches the surface of the liquid or bulk material, it is reflected off of it.
- The amount of energy reflected depends on the properties of the fluid or bulk material.
- For example, a smooth liquid will reflect more energy than a rough bulk material.
3. Receiving the reflected signal:
- The reflected signal is received by the sensor using a receiver.
- The receiver can be the same as the emitter or separate.
- The reflected an electrical signal is created from the signal.
4. Distance calculation:
- The sensor measures the time it took for the pulse to travel there and back.
- This time is utilized to determine how far away the sensor is to the surface of the liquid or bulk material.
- The distance calculation is based on the formula:
distance = (time * speed of sound) / 2
Where:
distance - the distance from the sensor to the surface of the liquid or bulk material
time - the time it took the pulse to travel back and forth
speed of sound - the speed of sound in the medium
5. Convert to a level signal:
- The calculated distance is converted to a level signal that can be used by a controller or other device.
- The level signal can be analog or digital.
- The analog signal represents the level with voltage.
- A digital signal represents the level in binary code.
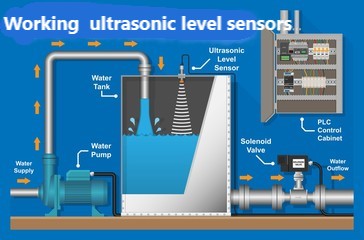
Important factors to consider:
- Sound velocity: The speed of sound varies depending on the temperature and properties of the medium. Some sensors are temperature compensated to ensure accurate gauging.
- Acoustic noise: Acoustic noise can affect measurement accuracy. Some sensors have filters to help reduce the effects of noise.
- Tank size and shape: The size and shape of the vessel can affect the propagation of ultrasonic waves. Some sensors are specially designed for level measurement in tanks with uneven walls or obstructions.
A dependable and precise method for determining the level of liquids or bulk solids is to employ ultrasonic level detector.
Ultrasonic Level Sensor Types Mainly
Industrial automation makes extensive use of ultrasonic level sensors to measure the level of various substances, offering a non-contact approach that minimizes contamination risks. When discussing the principle of operation of these sensors, it's important to understand that there are two main types: transmission-based and reflection-based ultrasonic level sensors. Each type operates on the same basic principle of using ultrasonic sound waves but has different methods for measuring the level of a substance. Let's dive into these two main types to understand how they work and what makes them unique.
1. Unidirectional level sensors
In unidirectional sensors, the transmitter and receiver are located opposite each other in the same tank wall.
Operation:
- An ultrasonic pulse directed perpendicular to the tank wall is produced by the transmitter.
- The pulse passes through the liquid or bulk material and is reflected from the surface.
- The reflected signal is received by the receiver.
- The sensor measures the time it took the pulse to move back and forth while figuring out how far the liquid's surface is away or bulk material.
Advantages:
- Simple design
- Low cost
- Suitable for level measurement in tanks with flat walls
Disadvantages:
- Not suitable for level measurement in tanks with uneven walls or obstacles
- May be less accurate than reflective sensors
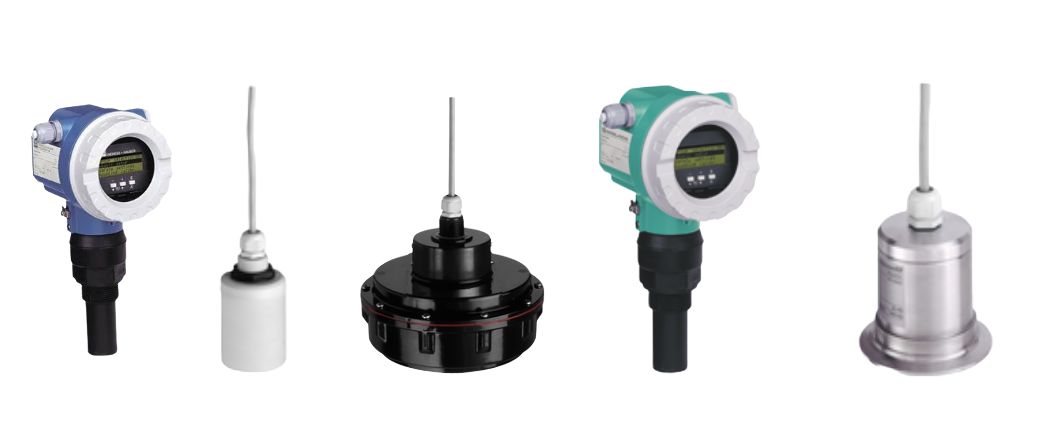
2. Reflective level sensors
In reflective sensors, the transmitter and receiver are located in the same housing, which is mounted on the tank wall.
Operation:
- An ultrasonic pulse produced by the transmitter is angled toward the tank wall.
- The pulse is reflected from the tank wall and then from the surface of the liquid or bulk material.
- The reflected signal is received by the receiver.
- The sensor measures the time it took the pulse to move back and forth while determining the liquid's surface distance or bulk material.
Advantages:
- Suitable for level measurement in tanks with uneven walls or obstacles
- Can be more accurate than unidirectional sensors
Disadvantages:
- More complex design
- Higher cost
- Can be larger than unidirectional sensors
Limitations and Challenges
Ultrasonic level sensors are invaluable in industrial automation for their non-contact measurement capability, allowing accurate level measurement across various industries. However, like any technology, they come with limitations and challenges. Understanding these limitations and knowing how to address them is crucial for successful implementation.
1. Installation and Calibration
Proper installation and calibration are essential to the operation of ultrasonic level sensors optimally. Incorrect installation can lead to inaccurate readings, while calibration issues may cause fluctuations in measurement. Here are some key considerations:
- Installation Position: Ultrasonic level sensors require an unobstructed view of the surface being measured. Ensure there's no obstruction in the sensor's path, such as internal structures or equipment.
- Calibration: Ultrasonic sensors often come pre-calibrated, but it's vital to check and adjust calibration during installation. Calibration involves setting the sensor's zero point (when it's not detecting any material) and full-scale point (when it's at maximum measurement range).
- Temperature and Humidity: These environmental factors can affect the speed of sound, leading to calibration issues. Some sensors have temperature compensation features, but it's crucial to account for variations during calibration.
2. Maintaining Ultrasonic Level Sensors
Maintenance plays a significant role in ensuring the accuracy and longevity of ultrasonic sensor. A well-maintained sensor is less likely to experience errors or malfunctions. Here's what you need to focus on:
- Regular Cleaning: The ability of the sensor to produce and receive ultrasonic waves may be impacted by dust, debris, or accumulation on its surface. Regular cleaning ensures optimal performance.
- Inspect Connections: Check wiring and connections for signs of wear, corrosion, or loosening. Faulty connections can lead to signal loss or erratic readings.
- Firmware Updates: Some sensors have firmware that may require updates to maintain compatibility with control systems and improve functionality. Keep the firmware updated as needed.
- Scheduled Calibration: Even if calibration was correct during installation, regular recalibration is necessary, especially in environments where an ultrasonic pulse produced by the transmitter is angled toward the tank wall.
3. Choosing the Right Sensor for Your Application
Selecting the appropriate ultrasonic level sensor is essential for accurate measurement and efficient operation. Different applications have varying requirements, and the wrong choice can lead to poor performance. Consider the following factors when choosing a sensor:
- Measurement Range: Determine the distance range your application requires. Ultrasonic sensor come in various ranges, so choose one that covers your needs without exceeding its limits.
- Accuracy Requirements: Some applications demand high precision, while others can tolerate more significant variation. Choose a sensor with the level of accuracy appropriate for your application.
- Material Compatibility: While level sensor work with many materials, some dense or highly viscous substances may pose challenges. Ensure the sensor is suitable for the material you'll be measuring.
- Output Options: Ultrasonic sensors offer different output types, such as analog, digital, or 4-20 mA signals. Ensure the sensor's output is compatible with your control system.
4. Common Problems and Troubleshooting
Despite their reliability, ultrasonic level sensors can encounter problems. Here are some common issues and troubleshooting steps:
- Erratic Readings: If the sensor gives inconsistent or fluctuating readings, check for obstructions in the signal path, ensure proper calibration, and inspect for environmental factors affecting performance.
- No Output Signal: This can result from faulty connections, power issues, or damage to the sensor. Check power sources, wiring, and the sensor for visible damage.
- Inaccurate Measurements: Inaccurate readings may indicate calibration problems or interference from temperature or humidity. Recalibrate the sensor and ensure it's operating within its environmental specifications.
- Sensor Damage: Physical damage to the sensor, such as cracks or deformations, can compromise its performance. Inspect the sensor regularly and replace it if necessary.
Understanding these limitations and challenges, along with best practices for installation, maintenance, and troubleshooting, is key to maximizing the performance and lifespan of ultrasonic level sensors in industrial automation. Proper attention to these aspects ensures that the sensors continue to deliver accurate and reliable measurements in various applications.
Future Advances in Ultrasonic Level Sensor Technology
The level of liquids or bulk solids can already be accurately and dependably measured using sensors for ultrasonic levels.
However, the technology is constantly evolving, and a number of new developments can be expected in the future that will make the sensors even better.
Here are some of the promising areas of development
- Improving accuracy: Researchers are working on new methods to improve the accuracy of ultrasonic level sensor. This may include developing new algorithms for signal processing, using higher frequency sensors, and improving temperature compensation methods.
- Increase the measurement range: The range of measurement for certain ultrasonic sensors is constrained. Researchers are working to develop sensors that can measure levels over longer distances.
- Expanding the possibilities: Ultrasonic level sensors are already used in various industries. Researchers are working on extending the capabilities of the sensors for new applications. This could include using the sensors to measure levels in hazardous or corrosive environments, as well as to measure the level of non-homogeneous liquids or bulk materials.
- Miniaturization: Ultrasonic level sensors are becoming smaller and lighter. This trend is likely to continue in the future, making the sensors more convenient for use in confined spaces.
- Wireless sensors: A few ultrasonic level detectors are already wireless. This trend is likely to become more common in the future, making the sensors easier to install and use.
- Integrated sensors: Ultrasonic level sensor can be integrated with other sensors and devices. This can make the sensors more versatile and efficient.
Ultrasonic level sensors are now an even more useful instrument for determining the level of liquids or bulk solids, thanks to these and other advancements.
Conclusion
Ultrasonic level sensors are essential in automation process, offering a non-contact technique to measure the amounts of liquid and solid. These sensors are versatile and reliable, making them appropriate for a variety of uses. Proper installation, calibration, and maintenance are crucial for accurate performance. Ultrasonic level sensors are predicted to improve in accuracy, efficiency, and IoT system integration as technology advances, increasing their usefulness in industrial environments.