Proximity sensor vs Photoelectric sensor
01.11.2023
Sensors are important components of any industrial control system as they provide input data to monitor and control various processes and machines. However, not all sensors are created equal, and choosing the right one for your project can be challenging. In this article, we will look at Proximity vs. Photoelectric sensors.
Significance of Sensor Comparison
Automation of production is a very painstaking task that must be approached responsibly. So it is very important for you to choose the right equipment that will exactly meet all your tasks and requirements. Sensors are also no exception. After all, if you choose a sensor that is not suitable for your needs, you will not get the desired result. That is why we have arranged a sensor comparison today.
How Proximity Sensors Work
Proximity sensors are electronic devices designed to detect the presence or absence of objects within their detection range without physical contact. The proximity sensor working principle consists of different principles, including electromagnetic, capacitive, inductive, and ultrasonic, depending on the type of proximity sensor.
How Photoelectric Sensors Work
Photoelectric sensors, also known as photoelectric sensors or photocells, are electronic devices that use light to detect the presence, absence, or specific characteristics of objects within their detection range. The photoelectric sensor working principle is to emit a beam of light and then measure changes in the resulting light to determine the presence or properties of an object. Photoelectric sensors are widely used in various industrial and automation applications due to their versatility and reliability.
Types of Proximity Sensors
Let's look at what types of proximity object sensing solutions exist.
Inductive proximity sensors
Inductive proximity sensors work on the principle of electromagnetic induction. They generate an electromagnetic field around a coil in the sensor's active face. These sensors are primarily used to detect metallic objects. When a metallic object enters the sensor's detection range, it disturbs the electromagnetic field, causing the sensor to trigger an output signal.
Capacitive proximity sensors
Capacitive proximity sensors operate based on changes in capacitance. They consist of two conductive plates with an insulating material in between.
Detection Target: These sensors can detect a wide range of materials, including liquids, solids, and powders, depending on their dielectric properties. When an object with dielectric properties enters the sensor's range, it alters the capacitance, triggering an output signal.
Ultrasonic proximity sensors
Ultrasonic proximity sensors use high-frequency sound waves (ultrasonic waves) to detect objects. They emit ultrasonic pulses and measure the time it takes for the pulses to bounce back (time-of-flight) to determine the distance to the object. These sensors can detect a wide range of materials, including solid objects, liquids, and even transparent materials.
Magnetic proximity sensors
Magnetic proximity sensors use changes in magnetic fields to detect objects. They consist of a permanent magnet and a Hall effect sensor. These sensors are typically used to detect ferrous (iron or steel) objects that can disrupt the magnetic field.
Laser proximity sensors
Laser proximity sensors emit a focused laser beam and measure the time it takes for the laser light to reflect off an object and return (time-of-flight). These sensors are used for precise and long-range detection of objects, often in applications requiring high accuracy.
Types of Photoelectric Sensors
Let's continue our sensor technology comparison with a list of existing photoelectric sensors.
Through-beam sensors
Through-beam sensors consist of a separate emitter and receiver. The emitter sends out a focused light beam, and the receiver is positioned opposite the emitter to detect the light. These sensors detect objects when they interrupt the light beam between the emitter and receiver.
Retroreflective sensors
Retroreflective sensors also have an emitter and receiver, but they use a reflector to bounce the emitted light back to the receiver. Objects are detected when they block the reflected light beam.
Diffuse-reflective sensors
Diffuse-reflective sensors combine the emitter and receiver in a single housing. The emitted light reflects off an object and back into the receiver. Objects are detected based on the amount of light reflected back to the receiver. These sensors have a defined sensing range.
Polarized retroreflective sensors
Similar to retroreflective sensors, these sensors use a reflector, but they emit polarized light. The receiver is equipped with a polarized filter to reduce false signals caused by reflections from shiny surfaces. Objects are detected when they block the polarized reflected light.
Background suppression sensors
Background suppression sensors emit a light beam with a known divergence angle. They are designed to detect objects at a specific distance while ignoring objects that are closer or farther away. Objects are detected when they reflect light back to the sensor within the specified distance range.
Transparent object sensors
Transparent object sensors are designed to detect transparent or translucent objects, such as glass or plastic. These sensors can detect the presence of transparent objects based on the refractive index difference between the object and the surrounding medium.
Advantages and Limitations
Below we will look at the advantages and limitations of proximity and photoelectric sensors.
Advantages of proximity sensors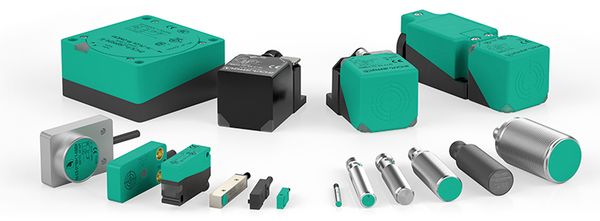
- Non-contact operation.
- Durability.
- Fast response.
- Long service life.
- Wide range of detection.
- Accuracy.
- Variability in sensing range.
- Digital and analog output.
- Energy efficiency.
Limitations of proximity sensors
- Material compatibility. The type of proximity sensor chosen should be compatible with the material or object to be detected. For example, inductive sensors are suitable for metallic objects but not for non-metals.
- Sensing range. The sensing range of proximity sensors is limited. Choosing the appropriate sensor with the right range is crucial for accurate detection.
- Interference. Proximity sensors can be susceptible to interference from nearby electrical equipment, electromagnetic fields, or other sensors. Proper shielding and isolation may be necessary to mitigate interference.
- Temperature and environmental considerations. Extreme temperatures and harsh environmental conditions can affect sensor performance. Specialized sensors may be required for such applications.
- Blind spots. Proximity sensors may have blind spots, which are areas where objects cannot be detected. Users must be aware of these limitations when designing their systems.
Advantages of photoelectric sensors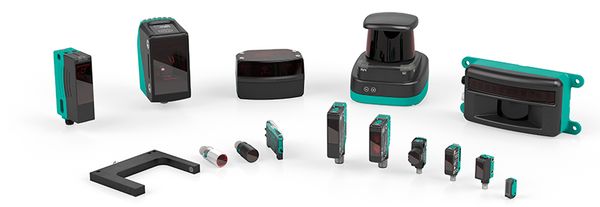
- Non-contact operation.
- Material versatility.
- Flexibility.
- Compact size.
- High-speed operation.
Limitations of photoelectric sensors
- Light conditions. Photoelectric sensors can be affected by ambient light conditions, including sunlight and other sources of interference. Proper shielding and filtering may be necessary.
- Reflectivity. The reflectivity of the object being detected can impact sensor performance, especially in retroreflective and diffuse-reflective modes.
- Limited detection range. The detection range of photoelectric sensors is typically limited compared to some other types of sensors.
- Alignment. Some photoelectric sensors, especially through-beam types, require precise alignment for reliable operation.
- Environmental factors. Harsh environmental conditions, such as extreme temperatures, can affect the performance of photoelectric sensors.
- Transparency. Transparent or highly translucent materials may not be reliably detected by certain photoelectric sensor types.
Eltra Trade offers a wide selection of sensors for various needs from leading companies like Balluff, IFM, Norgren, Omron, Pepperl+Fuchs and more. Our expert managers are ready to assist with selection and answer questions. Enjoy fast worldwide delivery and the best prices!