Baumer encoders: the best decision for heavy industry
01.03.2018
Baumer encoders are integral to the success of heavy industry, where precision and reliability are paramount. Encoders play a crucial role in converting mechanical motion into precise electrical signals, enabling accurate control and monitoring of machinery. In heavy industry, where equipment operates under extreme conditions, the need for durable, high-performance encoders is essential. Baumer encoders stand out as the best solution, offering unmatched accuracy, durability, and adaptability. They ensure that critical processes in industries like mining, manufacturing, and energy production run smoothly, reducing downtime and enhancing operational efficiency. Baumer's commitment to quality makes their encoders the ideal choice for demanding industrial environments.
Types of encoders and their applications
- Absolute Encoders: These encoders provide a direct digital readout of the shaft's position, regardless of its starting point.
- Incremental Encoders: As the shaft rotates, these encoders produce pulses that convey relative position data.
- Explosion-Proof Encoders: Designed for hazardous environments, these encoders are constructed with robust housings to prevent ignition.
- Tachogenerators and Resolvers: Measuring Rotational Speed and Position
Absolute Encoders
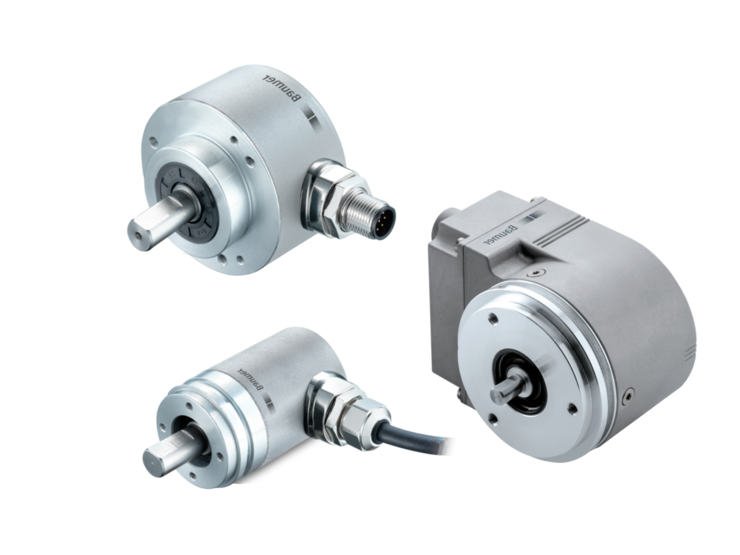
- Digital Interfaces: SSI, BiSS, CANopen, Profibus, PROFINET, EtherCAT, EtherNet/IP.
- Housing Sizes: Compact designs ranging from 28 mm to 58 mm.
- Material: Options include aluminum and stainless steel.
- Resolution: Up to 13 bits for singleturn and up to 16 bits for multiturn.
- Accuracy: Optical encoders up to ±0.01°, magnetic encoders up to ±0.15°.
- Speed: Maximum operating speeds up to 6000 rpm.
- Protection Ratings: IP54, IP65, and higher for dust and water resistance.
- Temperature Range: From -25°C to +85°C, with extended ranges available.
- Industry 4.0 Ready: Advanced connectivity options for smart factory applications.
- Redundant Variants: Available for critical applications requiring high reliability.
- High Accuracy
- Eliminates Homing
- Immediate Position Feedback
- Enhanced Reliability
- Versatility
- CNC Machining: Ensuring accurate tool positioning for precise machining operations.
- Robotics: Controlling the movement of robotic arms and joints for tasks such as assembly and material handling.
- Motion Control Systems: Giving servo motors and other motion control applications accurate position feedback.
- Automation Equipment: Controlling the positioning of various components in automated systems.
- Medical Devices: Used in medical equipment such as surgical robots and diagnostic devices for precise positioning and control.
- Factory Automation: Controlling the movement of machines and equipment in manufacturing processes.
Incremental Encoders
- Housing Sizes: Compact designs ranging from 24 mm to 85 mm.
- Resolution: Up to 65,536 pulses per revolution (ppr) for optical encoders.
- Accuracy: Optical encoders up to 30 arcseconds.
- Speed: Maximum operating speeds up to 12,000 rpm.
- Output Frequency: Up to 300 kHz.
- Voltage Supply: 5 VDC ±10%, 10…30 VDC.
- Output Signals: HTL, TTL, SinCos, quadrature, pulse & direction, index.
- Output Stages: Line driver/RS422, push-pull short-circuit proof.
- Protection Ratings: IP42, IP64, and higher for dust and water resistance.
- Temperature Range: From -20°C to +85°C.
- Vibration Resistance: Up to 10 g.
- Shock Resistance: Up to 50 g.
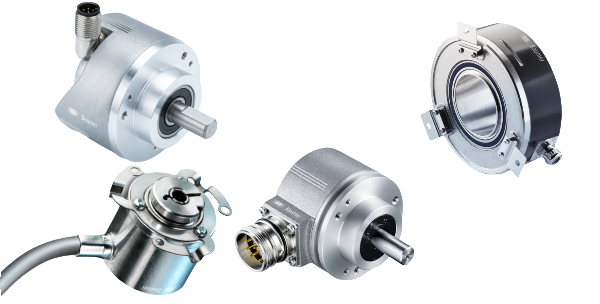
- Cost-Effective
- High Resolution
- Robust Construction
- Wide Range of Applications
- Motor Control: Controlling the speed and position of motors in various industrial processes.
- Speed Measurement: Measuring the rotational speed of shafts and other moving components.
- Positioning Systems: Accurately positioning components in various industrial machines and equipment.
- Robotics: Controlling the movement of robotic arms and joints.
- Factory Automation: Measuring the position and speed of machines and equipment in manufacturing processes.
- Machine Tools: Controlling the movement of machine tool components, such as spindles and tables.
Functional safety encoder
Position sensors that have been specifically engineered to be safe for use in potentially dangerous situations where explosive gasses or dusts may be present are known as explosion-proof encoders. To stop the surrounding air from igniting, these encoders are built with sturdy housings and seals.
Technical Characteristics
- Resolution: Up to 5000 pulses per revolution (ppr).
- Speed: Maximum operating speeds up to 6000 rpm.
- Output Frequency: Up to 300 kHz.
- Voltage Supply: 4.75…30 VDC.
- Output Signals: Push-pull short-circuit proof, RS422.
- Output Stages: Line driver/RS422, push-pull.
- Protection Ratings: IP67 for dust and water resistance.
- Temperature Range: Operating temperatures from -20°C to +70°C.
- Explosion Protection: Certified for Ex II 2G Ex d IIC T4/T6 and Ex II 2D.
- Shock Resistance: Up to 300 g, 1 ms.
- Vibration Resistance: Up to 10 g.
- ATEX Certification: Suitable for use in potentially explosive environments (Zone 1 for gas, Zone 21 for dust).
- Robust Design: Designed to withstand harsh industrial conditions.
Advantages of Explosion-Proof Encoders
- Safety
- Reliability
- Compliance
- Versatility
Applications of Explosion-Proof Encoders
Explosion-proof encoders are commonly used in industries where hazardous materials are present:
- Oil and Gas: Measuring the position of valves, pumps, and other equipment in oil and gas facilities.
- Chemical Processing: Monitoring the position of components in chemical plants and refineries.
- Mining: Measuring the position of machinery and equipment in underground mines.
- Pharmaceutical Manufacturing: Controlling the movement of equipment in pharmaceutical production facilities.
- Power Generation: Monitoring the position of components in power plants.
In dangerous locations, explosion-proof encoders are crucial parts that offer dependability and safety while guaranteeing adherence to industry standards. They are appropriate for many different applications because of their resilience and adaptability.
Tachogenerators and Resolvers
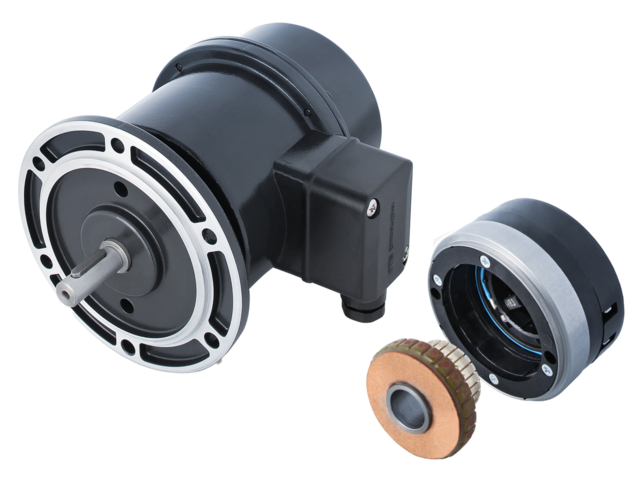
- Simple construction and operation
- Reliable and durable
- Wide range of operating speeds
- Motor control
- Tachometers
- Speed measurement
- Automotive applications
- High accuracy and precision
- Robust construction
- Suitable for high-speed applications
- Servo drives
- Motion control systems
- Robotics
- Aerospace applications
Advantages of Baumer Encoders
- High Accuracy: Baumer encoders provide exceptional accuracy, ensuring precise positioning and control in even the most demanding applications.
- Durability: Designed to withstand harsh industrial environments, Baumer encoders are built to last.
- Versatility: Baumer offers a wide range of encoder types, including absolute, incremental, and explosion-proof, to suit different needs.
- Reliability: Baumer's commitment to quality ensures consistent performance and minimal downtime.
- Global Presence: Baumer has a strong global presence, providing reliable support and service worldwide.
- Customization Options: Baumer can often customize encoders to meet specific application requirements.
- Reliable supplier: With years of experience in the industrial automation products market, Eltra Trade understands the unique requirements of its customers and provides exceptional support.